Introduction
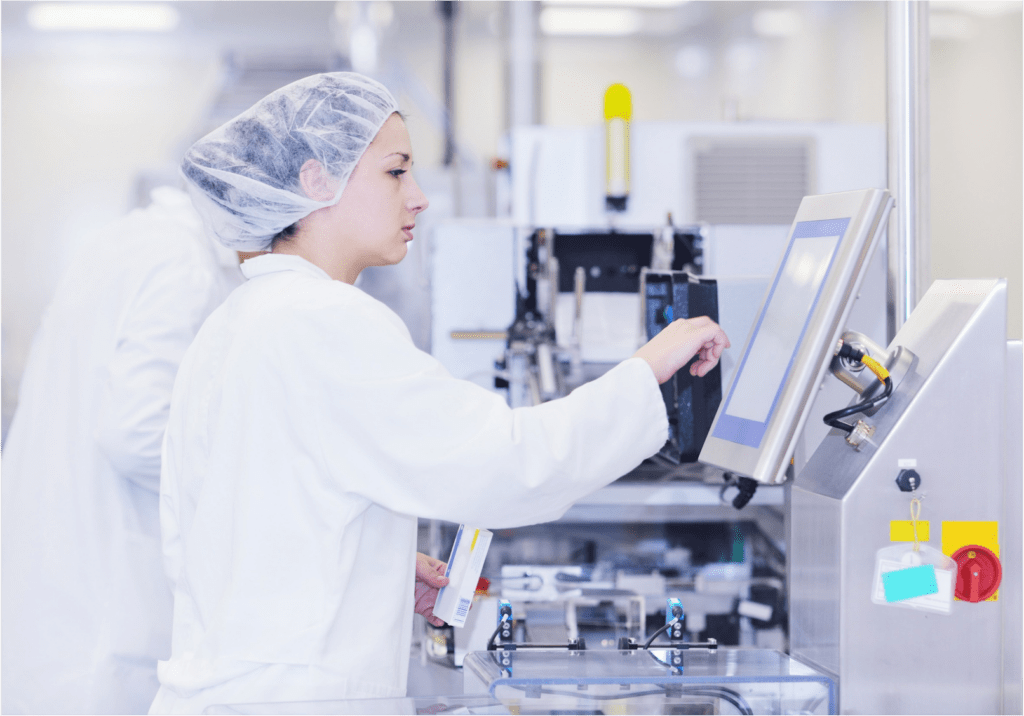
Some industrial sectors are subject to regulatory requirements related to their business (e.g. ISO standards, IFS …) or to the countries where they export their products (e.g. the 21-CFR-11 standard for the health and food industries in the United States). The transition from a traceability system based on paper form records to a digitalized system must be accompanied by a number of precautions.
We know that the computerization of the batch file is a transversal subject in companies and requires the collaboration of many departments. We know that the computerization of the batch file is a cross-cutting subject in companies and requires the collaboration of many departments. Many manufacturers in your sector of activity have improved their industrial performance and dematerialized their production information thanks to our MES Qubes solution. And this of course while respecting the regulatory constraints of their profession. In turn, you could computerize your production lines to set up an information system to automate and gradually dematerialize electronic batch files (DHR – Currency History Record or manufacturing file), perhaps still filled in on paper.
The main issues
- Compliance with current standards and regulatory constraints
- Gradually computerize the steps of constitution of the batch file to arrive at an electronic batch file
- Optimization of material flows and logistics management
- Provide a real-time management tool to gain responsiveness in the workshops
- Product quality control (Good Manufacturing Practices)
- Consolidate quality controls in production and laboratory
- Validation & Timestamp Workflow
- Reliability of data collection
- Electronic signature
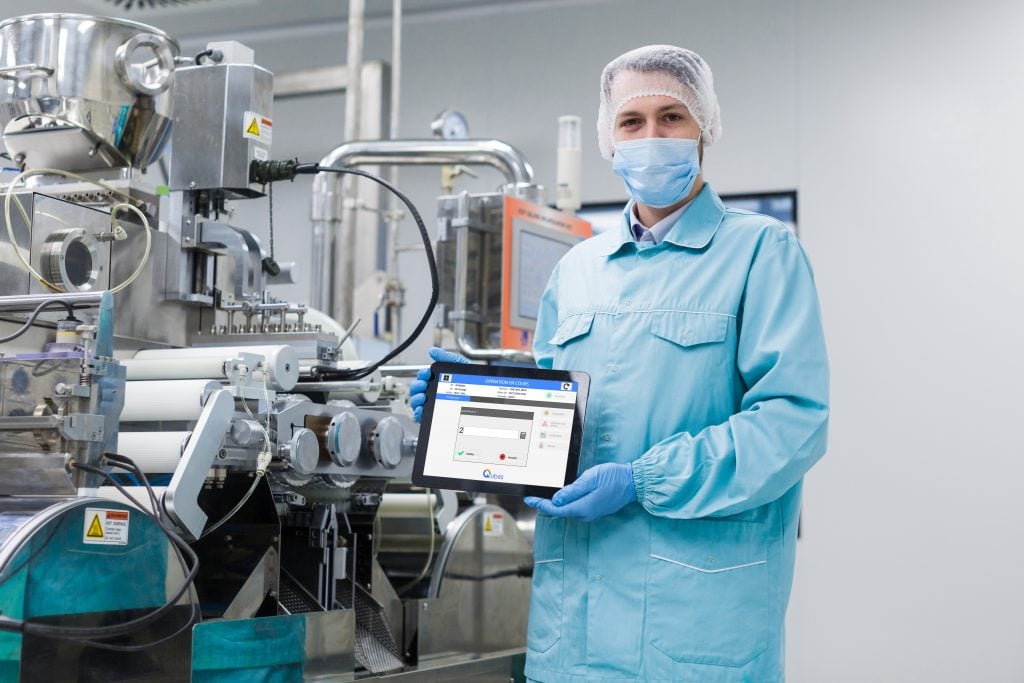
Features to discover
- Graphical workflow tool
- Document management
- Interfaces with ERP
- Factory Logistics
- Quality controls & administration of control plans